Welding Rotator Manufacturer & Supplier
WUXI ABK offers a full range of welding rotators with diverse load capacities to meet all your needs. We provide OEM and ODM services to elevate your business. As a leading welding rotator manufacturer with an expert technical team, we are your top choice for quality and innovation.
- The loading capacity ranges from 200kg to 2000 tons.
- Provide CE certification with a 13-monthly warranty.
- Working and providing a one-stop solution consulting for you.
- 24/7 customer service is available for concerns and inquiries.
WUXI ABK Welding Rotator
The welding rotator is a device used to rotate the cylindrical workpiece to realize efficient and automated welding.
Through the rotation of the roller, only the welding torch needs to be fixed at one point, and the automatic welding of the inner and outer circumferential seams and the inner and outer longitudinal seams can be realized.
No matter whether you are an end-user, distributor, or brand company, WUXI ABK will support you 100%. Great quality always with the appropriate price, WUXI ABK concerns more about our customers.
With more than 20 years of experience in the welding automation industry, we have been able to satisfy our customers, making a wide variety and range of welding rotators available.
Welding Rotator Production Details
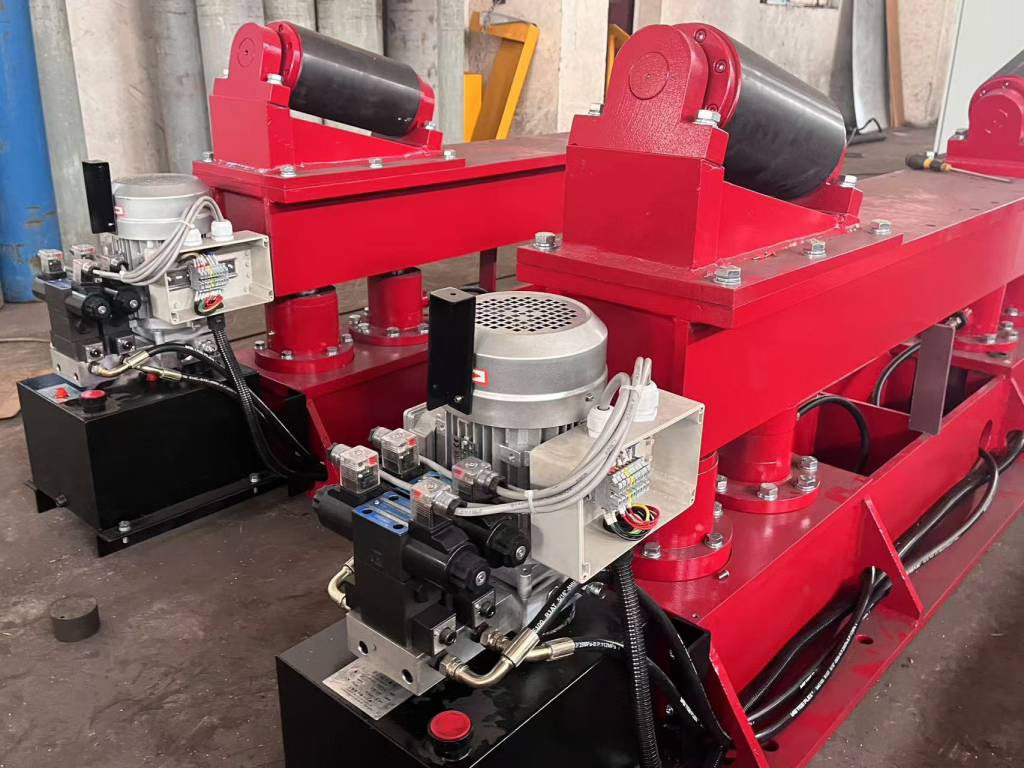
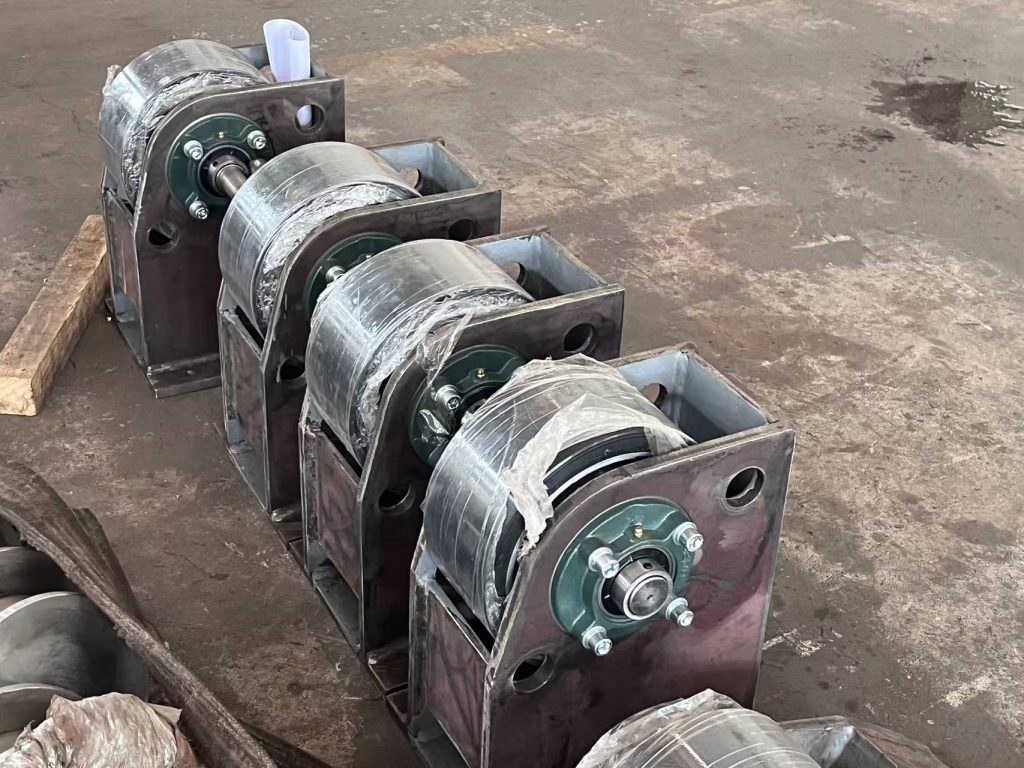
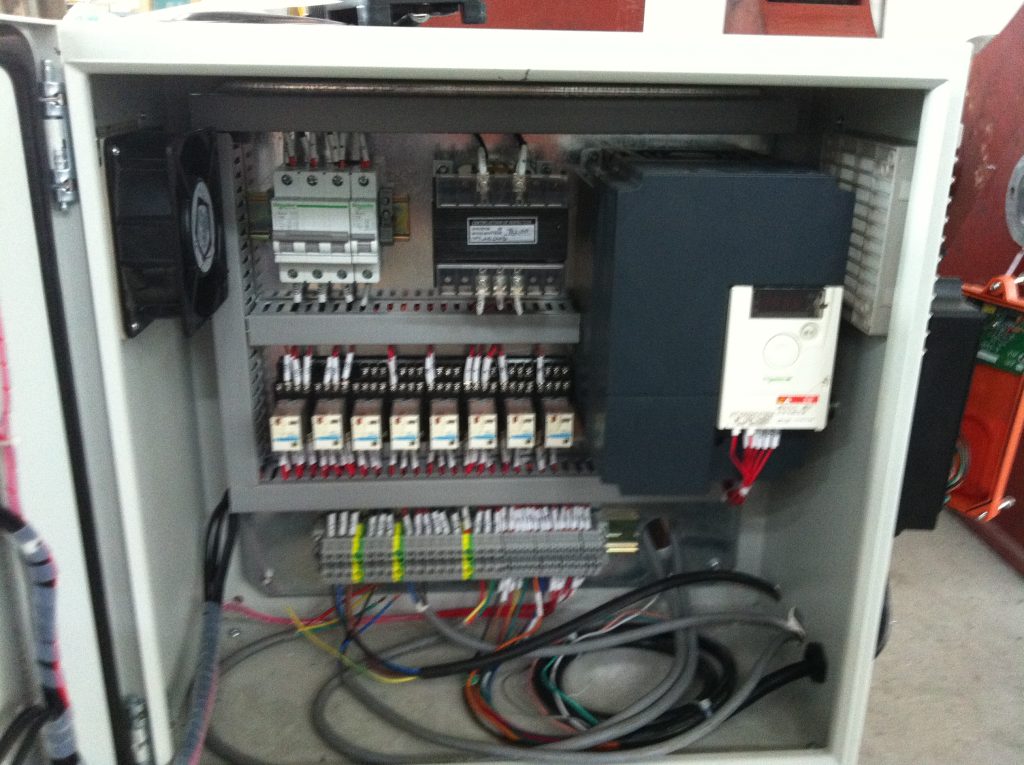
WUXI ABK Welding Rotator Advantages
Hight Quality
WUXI ABK understands trust comes from the quality and the value of the products.
High Output
We produce 100-300 welding rotators monthly, ensuring prompt delivery..
Warranty
We provide a one-year warranty with free replacement and wear part maintenance.
Technical Support
Experienced engineers with over 20 years of expertise are here to serve you.
High-standard Quality From WUXI ABK Welding Rotator
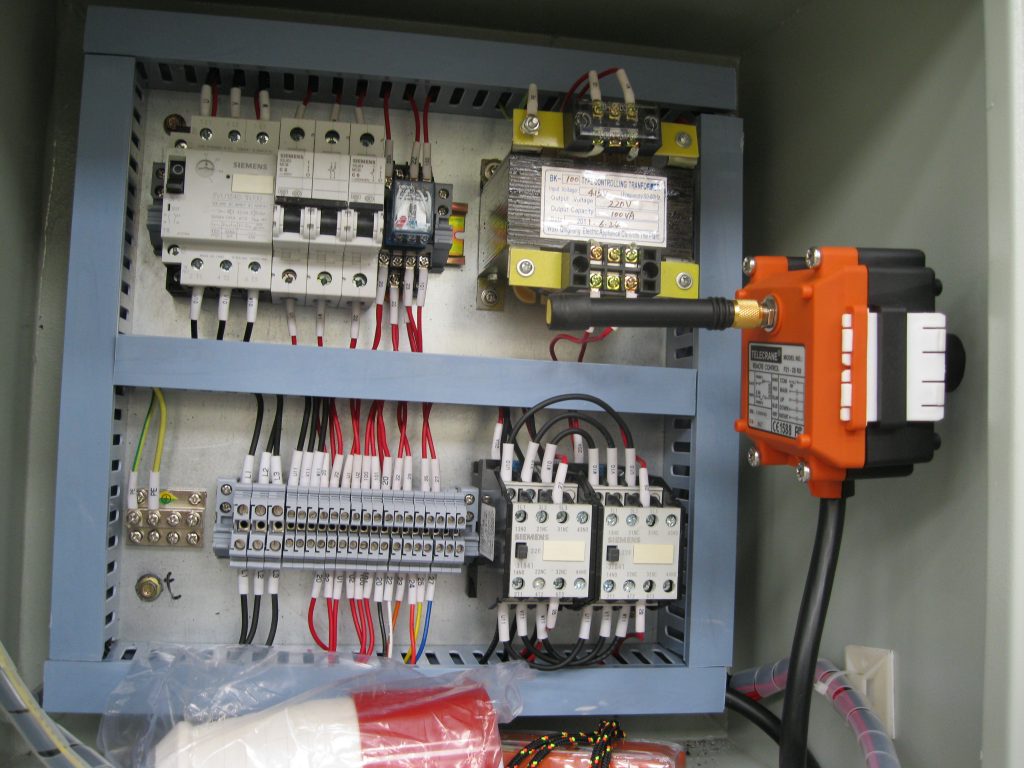
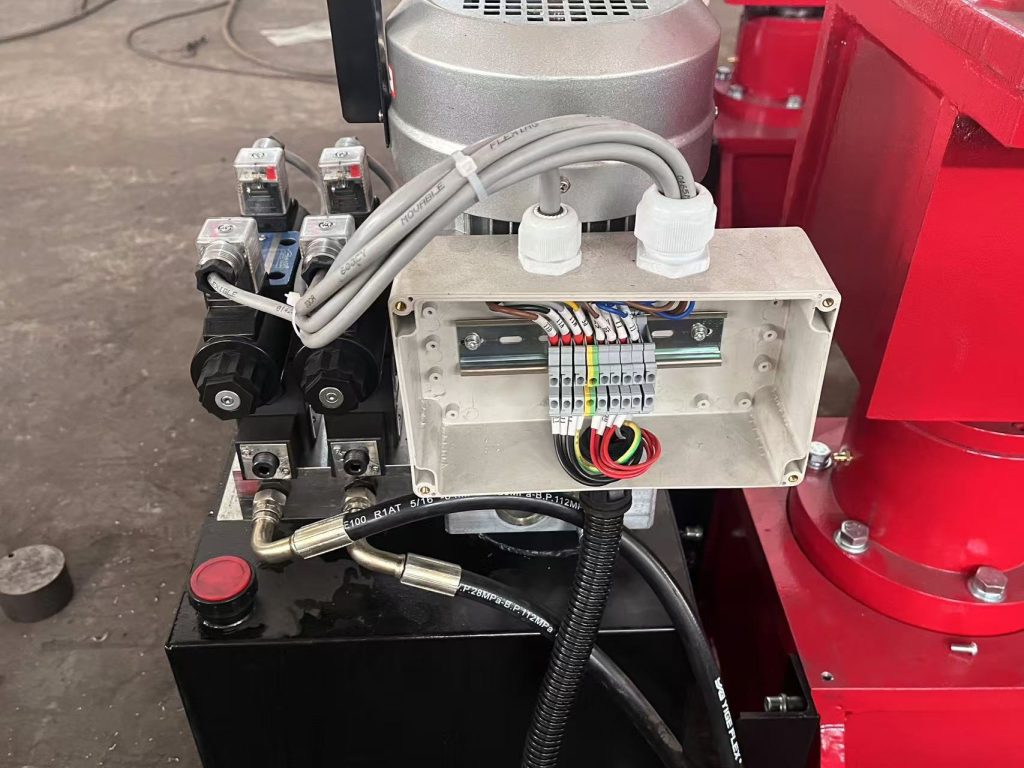
WUXI ABK upholds exceptionally high-quality standards in our manufacturing process. We consistently choose premium electrical components, such as Schneider or Danfoss, ensuring reliability and performance. Unlike some suppliers who compromise by using lower-quality brands to cut costs, we never take shortcuts.
Our commitment to quality extends to every aspect of production. We strictly adhere to the highest standards for raw materials, guaranteeing robust board thickness and optimal load capacities for all our equipment.
WUXI ABK is Your First Choice in Welding Rotator
With over two decades of welding rotator manufacturing experience, we bring satisfaction to our customers through manufacturing and also customization.
WUXI ABK cares about you and your company, we are good at welding rotator design, also we provide the best welding positioners for your welding.
Our newest arrivals
Model | HGZ-5 | HGZ-10 | HGZ-20 | HGZ-30 | HGZ-40 | HGZ-60 | HGZ-80 | HGZ-100 | HGZ-150 | HGZ-200 | ||
Loading Capacity (T) | 5 | 10 | 20 | 30 | 40 | 60 | 80 | 100 | 150 | 200 | ||
Workpiece Diameter | Min Diameter (mm) | 250 | 320 | 450 | 450 | 600 | 750 | 850 | 1000 | 1200 | 1500 | |
Max Diameter (mm) | 2300 | 2800 | 3500 | 3500 | 4200 | 4800 | 5000 | 5500 | 6500 | 8000 | ||
Rubber Roller | Diameter (mm) | 250 | 300 | 350 | 350 | 400 | 450 | 500 | 500 | 一 | 一 | |
Width (mm) | 100 | 120 | 120 | 120 | 120 | 120 | 120 | 120 | 一 | 一 | ||
Metal Roller | Diameter (mm) | 240 | 290 | 340 | 340 | 390 | 440 | 490 | 490 | 500 | 550 | |
Width (mm) | 15 | 25 | 30 | 30 | 40 | 50 | 60 | 70 | 260 | 260 | ||
Linear Speed (m/h) | 6-60 | |||||||||||
Speed Control | VFD Speed Control | |||||||||||
Motor Power (KW) | 0.75 | 1.5 | 1.5 | 2.2 | 3 | 4 | 4 | 5.5 | 5.5 | 7.5 | ||
Dimension | Drive Roller | Length (mm) | 1500 | 1800 | 2180 | 2180 | 2500 | 2780 | 3040 | 3450 | 3950 | 4300 |
Width (mm) | 800 | 830 | 960 | 960 | 1150 | 1240 | 1170 | 1400 | 1700 | 1800 | ||
Idler Roller | Length (mm) | 1350 | 160 | 1910 | 1910 | 2170 | 2400 | 2670 | 2930 | 3480 | 3800 | |
Length (mm) | 420 | 420 | 490 | 490 | 530 | 590 | 620 | 730 | 900 | 930 | ||
Height (mm) | 650 | 800 | 940 | 940 | 1030 | 1140 | 1200 | 1320 | 1550 | 1700 |
Model | HGK-2 | HGK-5 | HGK-10 | HGK-20 | HGK-30 | HGK-40 | HGK-60 | HGK-80 | HGK-100 | HGK-160 | HGK-200 | HGK-250 | HGK-300 | HGK-400 | HGK-500 | HGK-630 | HGK-800 | ||
Loading Capacity (T) | 2 | 5 | 10 | 20 | 30 | 40 | 60 | 80 | 100 | 160 | 200 | 250 | 300 | 400 | 500 | 630 | 800 | ||
Workpiece Diameter | Min Diameter (mm) | 200 | 250 | 320 | 500 | 550 | 600 | 700 | 700 | 700 | 1000 | 1000 | 1000 | 1000 | 1000 | 1000 | 1000 | 1500 | |
Max Diameter (mm) | 1800 | 2300 | 2800 | 3500 | 3800 | 4200 | 5000 | 5500 | 6000 | 6000 | 6000 | 7500 | 7500 | 7500 | 8000 | 8500 | 9000 | ||
Rubber Roller | Diameter (mm) | 200 | 250 | 300 | 350 | 350 | 400 | 450 | 500 | 500 | 一 | 一 | 一 | 一 | 一 | 一 | 一 | 一 | |
Width (mm) | 80 | 100 | 120 | 120 | 120 | 120 | 120 | 120 | 120 | 一 | 一 | 一 | 一 | 一 | 一 | 一 | 一 | ||
Metal Roller | Width (mm) | 190 | 240 | 290 | 340 | 340 | 390 | 440 | 490 | 490 | 550 | 550 | 700 | 700 | 800 | 800 | 850 | 1000 | |
Width (mm) | 15 | 20 | 25 | 30 | 35 | 45 | 60 | 70 | 80 | 260 | 260 | 260 | 260 | 300 | 300 | 350 | 350 | ||
Linear Speed (m/h) | 6-60 | ||||||||||||||||||
Speed Control | VFD Speed Control | ||||||||||||||||||
Motor Power (KW) | 2×0.18 | 2×0.37 | 2×0.55 | 2×0.75 | 2×1.1 | 2×1.5 | 2×2.2 | 2×3 | 2×3 | 2×4 | 2×4 | 2×5.5 | 2×5.5 | 2×5.5 | 2×5.5 | 2×7.5 | 2×7.5 | ||
Dimension | Drive Roller | Length (mm) | 1950 | 2090 | 2770 | 3150 | 3150 | 3300 | 4170 | 4370 | 4670 | 4900 | 4950 | 6500 | 6550 | 6600 | 6850 | 7200 | 7700 |
Width (mm) | 460 | 500 | 670 | 680 | 680 | 710 | 870 | 900 | 960 | 1000 | 1000 | 1000 | 1200 | 1280 | 1280 | 1450 | 1500 | ||
Idler Roller | Length (mm) | 1460 | 1800 | 2300 | 2450 | 2450 | 2900 | 3500 | 3700 | 4000 | 4000 | 4100 | 5500 | 5500 | 5500 | 5800 | 6000 | 6500 | |
Width (mm) | 280 | 300 | 400 | 520 | 520 | 530 | 650 | 700 | 760 | 800 | 800 | 920 | 950 | 1000 | 1000 | 1260 | 1260 | ||
Height (mm) | 350 | 430 | 510 | 680 | 680 | 680 | 830 | 890 | 960 | 1060 | 1080 | 1100 | 1300 | 1350 | 1350 | 1350 | 1550 |
Welding Rotator – The Ultimate FAQ Guide
A Welding Rotator is an auxiliary welding machine commonly used to weld round objects.
It will enable you to minimize tension, job toil, and manufacturing costs. They aid in the conservation of resources, allowing you to save money.
In this FAQ guide, we have covered everything you need to know about Welding Rotators.
A welding rotator is an essential piece of auxiliary equipment designed to rotate cylindrical workpieces, ensuring smooth and efficient welding operations. Depending on the adjustment method, welding rotators are categorized into self-aligning rotators and conventional rotators. Additionally, specialized types such as fit-up rotators, tank rotators, and track wheel rotators are available, tailored to meet specific workpiece requirements.
Key Components of a Welding Rotator
Welding rotators are composed of the following main parts:
- Base Foundation – Provides stability and support.
- Wheel Rollers – Positioned to hold and rotate the workpiece securely.
- Motor and Bearings – Drive the rotation and ensure smooth movement.
- Electric Box – Houses the control system for operation.
- Remote Control – Allows for convenient speed and direction adjustments.
For fit-up rotators, an additional hydraulic system is included to accommodate precise alignment and fit-up processes.
How Welding Rotators Work
A standard welding rotator setup includes one driving wheel and one idler wheel, with a total of four wheel rollers providing support and enabling rotation. The wheel material is chosen based on the specific characteristics of the workpiece to ensure compatibility and durability.
The operator can control rotation speed and direction—both forward and reverse—using a remote hand control or a foot panel, offering flexibility and precision in welding operations.
With its ability to streamline and enhance the welding process, the welding rotator is an invaluable tool for industries like oil and gas, manufacturing, and shipbuilding.
A welding rotator is designed to rotate cylindrical workpieces, such as pipes, tanks, or vessels, to facilitate efficient, precise, and uniform welding. Its operation relies on a combination of mechanical, electrical, and control systems working together to achieve smooth and controlled rotation. Here’s how it works:
1. Supporting the Workpiece
The workpiece is securely placed on the wheel rollers, which are specifically designed to provide stable support. The rollers’ material, such as rubber or steel, is selected based on the weight, size, and surface requirements of the workpiece to prevent slippage or damage.
2. Driving the Rotation
The driving wheel, powered by an electric motor, initiates the rotation of the workpiece. An idler wheel follows this motion, ensuring continuous support and smooth rotation. Together, these wheels ensure that the workpiece maintains its position during the process.
3. Speed Control and Adjustment
The speed of rotation is regulated using a variable frequency drive (VFD) or a similar control mechanism. Operators can adjust the speed to match the welding requirements through:
- A remote hand control for precise adjustments.
- A foot panel for convenient operation during welding.
This feature ensures compatibility with different welding techniques, such as MIG, TIG, or submerged arc welding (SAW).
4. Bidirectional Rotation
The motor allows the workpiece to rotate in both forward and reverse directions, depending on the welding sequence and project needs. This flexibility improves efficiency and enables easy reorientation for multi-pass welding.
5. Stability During Operation
The system’s motor and bearings work together to maintain consistent rotation, while the base foundation provides overall stability, even when handling heavy or oversized workpieces. This prevents vibrations or misalignment that could compromise weld quality.
6. Additional Features for Fit-Up Rotators
In fit-up rotators, a hydraulic system is integrated to allow precise alignment of the workpieces. This is especially useful for assembling and welding large-diameter sections, such as tanks or pressure vessels.
Benefits of the Welding Rotator’s Working Principle
- Improved Weld Quality: Consistent rotation ensures uniform welding with minimal defects.
- Increased Efficiency: Automating rotation reduces manual effort and speeds up production.
- Enhanced Safety: Secure handling of heavy components minimizes the risk of accidents.
- Versatility: Adjustable speed and direction make it adaptable to a wide range of welding tasks.
By leveraging its robust design and precision control, the welding rotator is an indispensable tool in modern welding operations across various industries.
Welding rotators are indispensable tools in various industries where precision and efficiency are essential for handling cylindrical workpieces. Their ability to rotate heavy components with stability and consistency makes them ideal for a wide range of applications, including:
1. Pressure Vessel Manufacturing
Welding rotators are commonly used in the fabrication of pressure vessels. They provide steady rotation for seamless welding, ensuring uniform joints and high structural integrity.
2. Oil and Gas Industry
In the construction of pipelines, tanks, and storage vessels, welding rotators play a crucial role. They enable the precise alignment and continuous rotation of pipes and tanks for smooth welding operations, even in large-scale projects.
3. Shipbuilding and Marine Engineering
The shipbuilding industry utilizes welding rotators for assembling and welding large cylindrical components, such as propeller shafts and fuel tanks, ensuring durability and accuracy in marine structures.
4. Wind Tower Production
Welding rotators are essential in the renewable energy sector for the construction of wind towers. Their capacity to handle massive, heavy sections facilitates efficient welding and assembly.
5. Boiler and Heat Exchanger Fabrication
In the manufacturing of boilers and heat exchangers, welding rotators ensure precise alignment and secure handling, contributing to high-quality welds and extended product lifespans.
6. Aerospace and Defense
In aerospace manufacturing, welding rotators assist in creating high-strength, lightweight cylindrical components, such as fuel tanks and structural parts, with superior weld quality.
7. Heavy Machinery and Industrial Equipment
Rotators are employed in the production of heavy machinery components, including rollers, drums, and cylinders, improving efficiency and reducing manual handling.
8. Chemical and Petrochemical Industries
Storage tanks and reactors used in the chemical and petrochemical sectors are often fabricated using welding rotators. Their precision helps meet the stringent quality standards required for these applications.
9. Water and Wastewater Management
The construction of large pipelines and storage tanks for water treatment and wastewater management benefits significantly from welding rotators’ ability to handle large-diameter workpieces efficiently.
10. Custom Fabrication and Prototyping
For specialized projects and prototypes involving unique cylindrical structures, welding rotators provide the flexibility and accuracy required to meet precise specifications.
By streamlining operations and ensuring consistent weld quality, welding rotators enhance productivity and safety in diverse industrial settings.
A Self-Aligning Welding Rotator is a high-precision welding auxiliary device designed to automatically adjust the alignment of cylindrical workpieces. It is widely used in welding and assembling large components such as tanks, pipes, boilers, and pressure vessels. The rotator features advanced mechanisms that allow it to adapt to varying diameters without manual intervention, enhancing efficiency and accuracy in welding processes.
Key Features:
- Automatic Alignment: Adjusts roller angles to fit workpieces of different diameters seamlessly.
- Robust Construction: Built with durable materials to handle heavy-duty applications.
- Variable Speed Control: Offers precise rotational speed adjustment to meet specific welding requirements.
- Load Capacity: Designed to support high-capacity loads for industrial projects.
- Compatibility: Ideal for use with automated welding systems, enhancing productivity.
Applications:
- Manufacturing of storage tanks and vessels
- Pipeline construction and welding
- Heavy equipment fabrication
Investing in a self-aligning welding rotator optimizes your production line, reduces manual effort, and ensures superior welding quality.
A Conventional Welding Rotator is a reliable and cost-effective tool for handling and rotating cylindrical workpieces during welding, assembly, and inspection processes. Unlike self-aligning models, these rotators require manual adjustment of the rollers to accommodate varying diameters, making them ideal for applications with consistent workpiece sizes or where manual control is preferred.
Key Features:
- Adjustable Rollers: Manually adjustable to fit different diameters of workpieces.
- Durable Design: Built to withstand heavy loads and rigorous industrial use.
- Steady Rotation: Provides smooth and consistent rotation for high-quality welding.
- Versatile Applications: Suitable for welding, assembly, and coating processes.
- Cost-Effective: A budget-friendly option for industries with stable size requirements.
Applications:
- Boiler and pressure vessel fabrication
- Pipeline welding
- Storage tank manufacturing
- Wind tower production
By integrating a conventional welding rotator into your production process, you gain a dependable solution for improving efficiency, ensuring precise rotations, and reducing operator fatigue. This equipment is a trusted choice for industries requiring straightforward yet robust welding support.
A Fit-Up Welding Rotator is an advanced welding auxiliary tool specifically designed to facilitate the alignment and positioning of multiple sections of cylindrical workpieces, such as tanks or pipelines, before welding. This type of rotator enables precise height and position adjustments, ensuring seamless assembly and high-quality welds.
Key Features:
- Height and Axial Adjustment: Allows precise alignment of adjoining workpieces to ensure a perfect fit.
- High Load Capacity: Built to handle large and heavy components with ease.
- Integrated Control Systems: Provides synchronized operation for efficient fit-up and welding processes.
- Customizable Design: Adaptable to various workpiece sizes and project requirements.
- Robust Construction: Ensures durability for demanding industrial applications.
Applications:
- Storage tank fabrication
- Large-diameter pipeline construction
- Wind tower assembly
- Boiler and pressure vessel welding
Advantages:
- Significantly reduces the time and effort required for manual alignment.
- Enhances welding accuracy and joint quality.
- Increases productivity by streamlining the fit-up process.
The Fit-Up Welding Rotator is an essential tool for industries requiring precision in assembling large, heavy-duty cylindrical components, providing both efficiency and reliability.
Self-Aligning and Conventional Welding Rotators are essential tools for rotating and positioning cylindrical workpieces, such as tanks, pipelines, and pressure vessels, during welding, assembly, or inspection. These two types of rotators serve distinct operational needs and can complement each other in versatile industrial applications.
Self-Aligning Welding Rotator
Designed for ease of operation and adaptability, self-aligning rotators automatically adjust the roller angles to accommodate workpieces of varying diameters.
Key Features:
- Automatic Diameter Adjustment: Adapts seamlessly to different sizes without manual intervention.
- Enhanced Productivity: Reduces downtime and increases efficiency.
- Smooth Operation: Provides steady rotation for precise and consistent welding.
- High Capacity: Suitable for heavy-duty applications.
Best For:
- Projects requiring frequent changes in workpiece diameters.
- Applications involving automated welding systems.
Conventional Welding Rotator
Conventional rotators offer manual adjustment of rollers, making them a cost-effective and straightforward solution for handling cylindrical workpieces.
Key Features:
- Manual Roller Adjustment: Allows for precise setup tailored to specific diameters.
- Durable Build: Capable of withstanding heavy industrial use.
- Affordable Option: Ideal for industries with consistent workpiece sizes.
Best For:
- Applications with steady workpiece sizes.
- Facilities seeking an economical option for simple rotations.
Comparison:
Feature | Self-Aligning Rotator | Conventional Rotator |
---|---|---|
Roller Adjustment | Automatic | Manual |
Adaptability | High (varied diameters) | Low (fixed sizes) |
Ease of Operation | Superior | Moderate |
Cost | Higher upfront investment | Budget-friendly |
Application Suitability | Versatile and automated | Stable and manual projects |
Choosing the Right Rotator:
- Opt for self-aligning rotators for dynamic projects requiring frequent adjustments and high precision.
- Select conventional rotators for budget-conscious operations with consistent workpiece dimensions.
Both types of rotators provide dependable solutions for improving welding accuracy, efficiency, and productivity, making them indispensable in modern fabrication processes.
A welding rotator is essential equipment for rotating and positioning cylindrical workpieces during welding. With its precise structure, a welding rotator ensures stability, efficiency, and high-quality results in various industrial applications. Below are the main components that make up a welding rotator.
The base frame of the welding rotator is its foundation, providing stability and minimizing vibrations. A strong base frame is crucial for supporting the weight of the entire welding rotator and the workpiece.
The driving unit is a key part of the welding rotator, consisting of a motor and gearbox that provide rotational power. This component ensures smooth and adjustable operation, making the welding rotator adaptable to various welding tasks.
The idle unit complements the driving unit, supporting the workpiece and ensuring balanced rotation. This structural feature helps the welding rotator handle heavy loads efficiently.
Rollers are another critical component of the welding rotator. These rollers, made from durable materials such as rubber, polyurethane, or metal, ensure secure and steady rotation of the workpiece. Roller brackets hold the rollers and allow the welding rotator to adjust to different diameters.
The control system is the operational core of the welding rotator. It allows for precise speed and direction adjustments, ensuring the welding rotator performs accurately. Self-aligning welding rotators automatically adjust roller angles, while conventional welding rotators require manual alignment.
The power supply unit provides the energy needed for consistent and reliable operation of the welding rotator.
In conclusion, the welding rotator, with its base frame, driving unit, idle unit, rollers, and control system, is indispensable in industrial welding. Its robust structure and adaptability make the welding rotator a critical tool for achieving precision, efficiency, and superior welding quality.
Proper maintenance of a welding rotator is essential for ensuring its optimal performance, longevity, and safety. Regular upkeep minimizes downtime and maximizes the efficiency of the welding rotator in industrial applications. Below are the key maintenance practices for a welding rotator.
1. Inspection of Rollers
The rollers of a welding rotator are crucial for holding and rotating workpieces. Regularly inspect them for wear, cracks, or deformation. Clean the rollers to remove dust, grease, or welding residues that may affect the grip. Replace damaged rollers promptly to avoid operational issues.
2. Lubrication
Proper lubrication of moving parts, such as bearings and gears, ensures smooth operation. Check the lubrication points specified in the welding rotator manual and apply grease or oil as required. Insufficient lubrication can lead to increased friction and component wear.
3. Alignment Checks
For both self-aligning welding rotators and conventional welding rotators, ensure that rollers and other components are correctly aligned. Misalignment can cause uneven rotation, damaging the workpiece or the rotator itself.
4. Electrical System Maintenance
Inspect the electrical system of the welding rotator, including motors, control panels, and power cables. Look for signs of wear, loose connections, or overheating. Ensure the control system operates smoothly, allowing precise adjustments to speed and direction.
5. Load Testing
Periodically test the welding rotator under its maximum load capacity to verify its performance. Avoid overloading, as it may damage the motor, rollers, or base frame. Ensure the load distribution is even to maintain balance during operation.
6. Cleaning
Keep the welding rotator clean and free from welding spatter, grease, and dust. A clean welding rotator operates more efficiently and reduces the risk of damage to components.
7. Regular Inspections
Schedule routine inspections to identify potential issues before they become major problems. Inspect all structural parts, including the base frame, roller brackets, and driving unit, for signs of damage or wear.
8. Replacement of Worn Parts
Replace worn or damaged components, such as rollers, belts, or bearings, promptly. Using a welding rotator with compromised parts can lead to poor performance or safety risks.
9. Calibration
For advanced welding rotators with automated features, periodically calibrate the control system to maintain accuracy. Calibration ensures precise speed and alignment adjustments.
10. Operator Training
Train operators to use the welding rotator properly and recognize early signs of wear or malfunction. Proper handling extends the lifespan of the equipment.
In conclusion, regular maintenance of a welding rotator is crucial for sustaining its performance and durability. By focusing on cleaning, lubrication, inspections, and timely replacements, a welding rotator can provide reliable service for years, ensuring efficiency and safety in welding processes.
Accidental damage to a welding rotator can lead to costly repairs, downtime, and compromised safety. By taking proactive measures, you can prevent damage and extend the lifespan of your welding rotator. Here are some essential tips to avoid accidental damage:
1. Proper Load Handling
Always ensure that the welding rotator is not overloaded beyond its specified capacity. Overloading can strain the motor, rollers, and gears, leading to premature wear or catastrophic failure. Ensure the load is evenly distributed to maintain balance and stability during operation.
2. Correct Setup and Alignment
Before operating the welding rotator, ensure that the rollers and other components are correctly aligned. Misalignment can cause uneven rotation and put additional stress on the welding rotator, increasing the risk of component failure. For self-aligning welding rotators, ensure the automatic adjustments are functioning properly.
3. Regular Inspections
Inspect the welding rotator regularly for any signs of wear, cracks, or loose components. Pay particular attention to the rollers, roller brackets, and the driving unit. Early detection of damage can prevent it from worsening and causing more significant issues.
4. Avoid Sharp Impacts
Avoid dropping heavy tools or equipment onto the welding rotator, as this can cause physical damage to the structure, rollers, or electrical components. Handle the equipment carefully to prevent unnecessary impacts or abrasions.
5. Proper Lubrication
Inadequate lubrication can lead to friction and overheating, which can cause components to wear out or break. Ensure the welding rotator is well-lubricated according to the manufacturer’s guidelines, particularly in areas with moving parts like gears and bearings.
6. Keep the Area Clean
Maintain a clean work area around the welding rotator to avoid foreign objects, welding spatter, or debris getting into the equipment. Contaminants can damage sensitive parts, reduce operational efficiency, and create safety hazards.
7. Avoid Sudden Movements
When starting or stopping the welding rotator, do so gradually to prevent sudden jerks or shocks that could damage the internal components. Always follow the manufacturer’s recommended startup and shutdown procedures.
8. Prevent Electrical Surges
Protect the welding rotator from power surges or electrical faults. Use surge protectors or circuit breakers to safeguard the electrical components and prevent accidental damage caused by power fluctuations.
9. Operator Training
Ensure all operators are properly trained on the correct operation and safety protocols for the welding rotator. A well-trained operator is less likely to make mistakes that could result in accidental damage.
10. Proper Storage
When not in use, store the welding rotator in a safe, dry location away from harsh environments. Exposure to extreme temperatures, moisture, or corrosive substances can lead to damage over time.
By following these guidelines, you can avoid accidental damage to your welding rotator, ensuring safe and efficient operation. Regular maintenance, careful handling, and operator awareness are key to extending the life of this crucial welding equipment.
Both welding rotators and welding positioners are essential tools in modern welding processes, but they serve different purposes and are designed for distinct tasks. Understanding the differences between them helps in choosing the right equipment for specific welding applications.
Welding Rotator
A welding rotator is used to rotate cylindrical workpieces, such as pipes, tanks, or pressure vessels, during the welding process. It helps position the workpiece for welding, ensuring smooth rotation and accurate welds.
- Function: Primarily rotates the workpiece along its axis for continuous welding.
- Usage: Ideal for large, cylindrical parts that require rotational positioning during welding.
- Adjustability: Often features adjustable rollers or self-aligning systems to accommodate various workpiece diameters.
- Operation: Works by rotating the workpiece at a consistent speed while welding. The rotation improves weld uniformity and reduces operator fatigue.
- Applications: Commonly used in pipe welding, tank fabrication, and pressure vessel production.
Welding Positioner
A welding positioner holds the workpiece in a fixed position and allows it to be tilted or rotated for optimal welding angles. It provides more control over the orientation of the workpiece, improving welding accuracy and efficiency.
- Function: Positions and tilts the workpiece at the optimal angle for welding.
- Usage: Best for welding small to medium-sized parts that require precise orientation and stable positioning.
- Adjustability: Often features tilting and rotating capabilities, allowing workpieces to be positioned at various angles for optimal weld accessibility.
- Operation: Typically uses a rotating table or head, along with tilting mechanisms, to adjust the angle of the workpiece.
- Applications: Commonly used in the fabrication of small components, brackets, or machinery parts that require accurate angle welding.
Key Differences
Feature | Welding Rotator | Welding Positioner |
---|---|---|
Primary Function | Rotates workpieces for continuous welding | Positions and tilts workpieces for optimal welding angles |
Adjustability | Adjustable rollers or self-aligning systems | Tilting and rotating mechanisms for precise positioning |
Ideal Workpieces | Cylindrical workpieces like pipes and tanks | Small to medium parts needing specific welding angles |
Applications | Pipe welding, tank fabrication, pressure vessels | Component welding, machinery parts, brackets |
Movement Type | Continuous rotation along the workpiece’s axis | Rotation and tilting for angle adjustments |
Common Features | Rollers, motorized driving unit, control system | Rotating table, tilting head, control system |
Conclusion
While both welding rotators and welding positioners enhance welding precision and efficiency, they are designed for different types of workpieces and applications. Welding rotators are ideal for rotating large cylindrical parts, such as pipes and tanks, during welding, while welding positioners are better suited for tilting and rotating smaller parts to achieve the correct welding angle. Depending on the type of project, selecting the right equipment ensures optimal results and improved productivity.